Wire and Cable extrusion
FIND OUT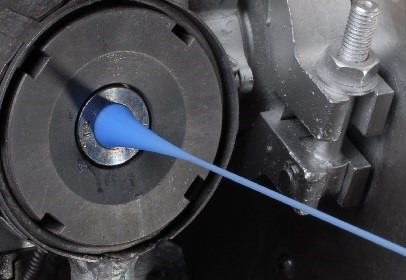
Extrusion is a process used to create objects with a fixed cross-sectional profile. A material is pushed through a die with the desired cross-section. The extrusion process can be done with the material hot or cold.In a subsequent stage, molten plastic is applied to the entire circumference of the wire, forcing it to adhere to the structure of the wire or cable. Extrusion is most commonly used for wire insulation and to form the outer sheath of the cable.
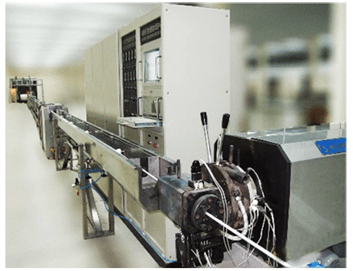
Drawing is a similar process, which uses the tensile strength of the material to pull it through the die. This limits the amount of change that can be performed in one step, so it is limited to simpler shapes, and multiple stages of decreasing size are usually needed. Drawing is the main way to produce wire. Metal bars and pipes are also often drawn. Drawing is usually done at room temperature.
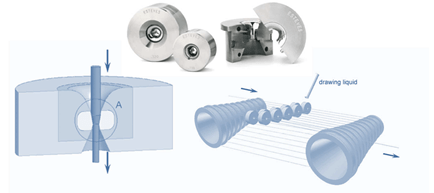
What are the processes commonly used?
Wire and Cable Extrusion is the process of converting plastic raw materials into a continuous profile, providing protection against external damage and physical wear. Different processes exist depending the different compounds requested by the market. The most commonly used process is for thermoplastic and thermosetting materials, where an internal machine (barrel) friction and external heat resistors are used to obtain a finished or semi-finished product, shaping material by forcing it through a die. Another process exists for rubber extrusion with many different vulcanization solutions engineered to heat the insulation after the die trough.
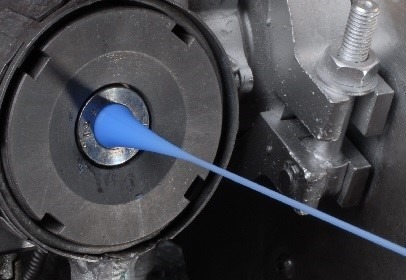
Extrusion quality controlTo ensure good wire coating extrusion quality, it is essential to identify, control, and monitor many parameters like pressures, die quality, operating conditions, and material in-feed. Various defects in the extrusion process must be identified to reduce their impact on product quality. Defects can be caused by a single source or the cumulative effect of several factors, which may arise at any stage of the processing. Rough surface, thickness variation, uneven wall thickness, diameter variation, and a centering problem are some of them.
Here we will mainly discuss the problems of the final geometries of wires, cables and tubes. There are many measuring devices on the market for measuring the outside diameter (OD). They generally have the same non-contact measuring technology with 2 perpendicular measuring axes. Some of the more advanced devices also come with 3 or even 4 axes of measurement. The aim is to provide manufacturers with a continuous measurement of the diameter and ovality of the extruded product. For the detection of fast defects such as Lumps & Neckdowns, some gauge manufacturers have a dedicated additional device.
CERSA, with its mastery of fast optical and electronic systems, offers an all-in-one solution. Our LPS (Laser Projection Sensor) measuring device allows you to control the diameter of the extruded product on 3 independent axes and also works as a flaw detector. With 20,000 measurements per axis per second it is able to detect very small and very short geometrical defects even on very fast extrusion lines. Its performance is 10 to 20 times faster than competing products. This device will soon be replaced by a higher-performance version for a wider range of diameters: the DLN.
To find out more :
To discover the DLN : click here
For all our other wire/cable/tube solutions : click here
And for the ideal solution for your business : click here or write to us directly at sale@cersa-mci.com
For the fine wire drawing process, CERSA also has a specific range of instruments with 1 or 2 measuring axes.
Our articles related
Contact the company CERSA MCI
Do you have a specific control and measurement need?
Are you looking for a high-performance control device?
You wish to request one of our services?